Articles
The Key to Implementing a Successful Predictive Maintenance Strategy
The data revolution of the manufacturing industry, Industry 4.0, has enabled a multitude of data driven processes to thrive, creating today’s Smart Factory. One of the first processes to flourish from this influx of data was Predictive Maintenance (PdM). Using asset specific data to predict where, when and why a specific asset will fail has been proven to save organisations millions by avoiding downtime and unnecessary repairs and replacements.
This has encouraged many solutions and approaches for PdM to evolve. Ensuring the approach you choose is a success can be achieved if you fully understand the intricacies of PdM, have the wisdom to think big but start small, have clear success criteria and build a comprehensive corporate wide roadmap.

Understand how Predictive Maintenance is different
Unlike traditional maintenance methods, PdM incorporates an array of data from all of your assets including asset specific usage, wear and conditional data, from both historic and real time sources, to predict where, when and why a fault will occur. PdM uses Data Mining and Predictive Algorithms to identify hidden patterns from all of your operational, usage and maintenance data files to predict a failure and prescribe the most appropriate repair or replacement work order. Advanced notice of impending failures allows time for these prescribed maintenance interventions to take place and prevent any failures occurring, keeping lines up and running smoothly. Using your own operational and usage data with these advanced algorithms is what separates PdM from the traditional maintenance approaches such as Preventative Maintenance, which has dominated the manufacturing world for the past two decades as the industry standard approach to maintenance.
Based on manufacturers’ recommendations on when to repair or replace parts and systems before they fail, Preventative Maintenance varies significantly from the realities of everyday operational usage. Each asset and system is subject to its own set of conditions, quirks and experiences, which the average lifetime estimations used in preventative maintenance strategies do not consider. This leads to very high level recommendations and suboptimal estimates for maintaining assets. Experienced technicians are required to interpret these high level recommendations, compare with usage reports, and more often than not rely on their gut instincts when deciding on how to proceed. Excluding your own operational and usage data from these recommendations and relying on gut feel, results in good parts being replaced too soon, and others failing before the recommended replacement schedule. Preventative Maintenance carries a lot of waste in the form of unnecessary maintenance interventions, nonessential part replacements and increased labour costs.
A number of organisations, especially regulated organisations, use Statistical Process Control (SPC) to trigger Preventative Maintenance interventions. Although SPC is more advanced than Preventative Maintenance, since it monitors the behaviour of your assets, it is not as comprehensive as PdM as it requires you to define your own upper and lower boundaries of acceptable operation for each asset. Define these too far out and you risk damaging both your assets and your products, define them too narrow and alarms will go off unnecessarily leading to a common preconception that all alarms are false alarms. A preconception that all alarms are false alarms means that real alarms are not managed as quickly as they should be. PdM not only adjusts the optimal upper and lower limits itself for optimum usage, but it also incorporates how the behaviour of other assets impacts the behaviour of the asset it’s monitoring.
With the increasing effect of Big Data instrumentation and the Internet of Things (IoT), more conditional, usage and wear data exists on assets today. There is now the opportunity to move away from traditional maintenance methods and use the full extent of the data you have available. Combining Big Data instrumentation and IoT data with historical maintenance logs and engineering data, produces more comprehensive and more accurate predictions on when and where faults or failures are most likely to occur. This then provides you with the advantage of having time on your side to proactively conduct the repair when it best fits within your operational schedule to minimise downtime and its knock on effects. You can even build this optimisation into your PdM strategy so that when faults are identified, the most appropriate action, work order or parts order, can be recommended through your existing asset management system.
Start small and build momentum
Before you start, it is important to identify your top business goals, your priority assets and where the relevant data exists. Generally there are 2 types of assets, the old clunky ones that have very little available data and the new robots that have lots of available data. Usually, the older ones are where the issues arise, however, with the cheap and easy to integrate instrumentation available today, it is now much easier to gather and store usage data on your older clunky assets.
By producing a matrix of how your different business goals align to operational readiness, data availability and business alignment, you can prioritise the most appropriate assets to begin with.
This way you can start small to pilot the solution and confidently assess the accuracy and effectiveness of your PdM strategy. Following an initial pilot project you can implement any necessary improvements and quickly identify the impact it is having on your business. You will then have the momentum you need to expand this new capability across the business.
Set evaluation criteria for continued success
PdM is money up front. You need to know what criteria have to be achieved in a certain time frame in order to get your return on investment (ROI). Is it 20 circumvented failures on the main production line? Is it the ability to order key parts far enough in advance that you avoid downtime entirely? Having clear objectives governing your ROI ensures your ability to measure the success of your PdM strategy from day 1 onwards.
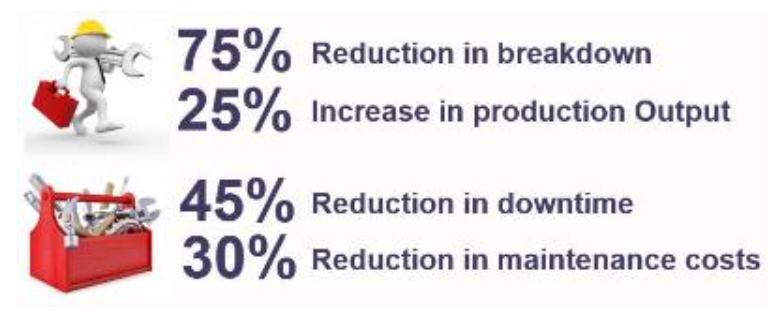
Continued monitoring, reviewing and updating is crucial for keeping your PdM strategy on track. A KPI or RoI Tracker can help you measure your success criteria. Continued measurement enables you to rate the success of your implementation and advance your PdM strategy to continually meet the demands of your changing business.
Know where you want to get to
In order to sustain your PdM strategy, there needs to be a long term development roadmap. Identifying the key corporate and operational goals you want to achieve is only step 1. Progressively building a comprehensive roadmap based on these goals is vital for the long term development and sustainability of your PdM strategy. Opening up PdM to all of your key assets by bringing IoT instrumentation on board can streamline your entire maintenance process. It allows the system to not only monitor usage data for maintenance requirements, but it also facilitates early warning notifications for any quality issues that may occur due to machine behaviour. By building key business goals into your PdM development roadmap, you can optimise your entire manufacturing process, maximising production demands, improving asset lifetime and avoiding potential warrantees. Start from the end goal and work backwards to know where to start.
Get the right people involved
The most likely cause of failure is not having the key stakeholders fully engaged with the strategy. From the board members to the machine operators, all participants need to be involved in the strategy and know how it will affect their role within the organisation. This involves identifying a strategy owner, who is then responsible for the communication and coordination of the strategy, ensuring change management steps are included in the strategy for all key stakeholders in the chain of command.
To produce effective predictions, you will need to consult with a data mining specialist to design the right modelling approach for your assets. All assets have different quirks, usage and functionality. Ensuring your predictive models account for these distinctive elements is key to improving the accuracy of your predictions.
You will also need engineers on board to ensure smooth integration and deployment of the predicted results. Predictions can be fed directly into your asset management system to automatically recommend the most optimised work orders. Keeping this integration as smooth as possible helps ensure successful deployment across the business and safeguards you from delays. Having a fully automated solution enables easy monitoring and measuring to track the success of your implementation.
Ensuring you have the right team in place, you have a comprehensive roadmap for where you want to get to and you have a clear set of success criteria, you will be able to sustain and proactively advance your PdM strategy. Following these steps will help safeguard the success of your PdM strategy and allow you to continually meet the demands of your changing business.
Version 1’s experienced consultants are on hand to help you understand your SPSS needs – from consultancy and training to finding the best software and license type for your analytical and usage requirements. Contact us to discuss your requirement and identify the best SPSS solution for you.
Related Articles
Take a look through our SPSS Articles covering a broad range of SPSS product and data analytics topics.